Lean production Lean production mode originated from Toyota production mode. It was concluded by experts and scholars from 17 countries in the world organized by Massachusetts Institute of technology in the United States. It took 5 years and 5 million US dollars to take the automobile industry, a typical industry that created mass production mode and lean production mode JIT, as an example.
Scheme definition Lean production solution, also known as APS+MES system (Advanced scheduling system + manufacturing execution system), is based on the manufacturing process of different industries, can selectively integrate system management software and human-machine interface equipment (PLC touch screen), LED production Kanban, LCD billboards, PDA smart handheld terminals, industrial tablet PCs, bar code collectors, sensors, I/O, DCS, RFID, industrial AP, WIFI and other types of integrated intelligent integrated systems. It consists of a set of shared data programs, through dedicated equipment placed at the production site, and through the embedded software to collect data, monitoring, control and intelligent analysis of the entire production process from raw material to finished product storage. It controls plant resources such as materials, warehouses, equipment, personnel, quality, processes, anomalies, process instructions and other facilities to increase productivity. Applications: Manufacturing companies.
Lean production solution based on the idea of lean production has a complete set of operation command, control, analysis and decision-making system, including self production scheduling, production site equipment control, process control, quality control, manufacturing progress control, on-site inventory, all kinds of data collection and analysis, material tracking, equipment automation transformation, etc., to further realize the detailed plan on the basis of automation. Decomposition, arrangement and implementation, feedback, business analysis, process analysis, process analysis, quality analysis, exception control, electronic Kanban display, communication reflection and a series of super functions, which can be customized according to the process of manufacturing enterprises.
Scheme index Production cycle is shortened by 35%; data input time is shortened by 36%; WIP is reduced by 32%; paperwork is reduced by 90%; delivery time is shortened by 22%; unqualified products are reduced by 22%; paperwork loss is reduced by 95%; information feedback efficiency is increased by 3860 times.
Scheme characteristics Lean production solution (APS + MES system) can help enterprises quickly realize flat organization, agile response, fewer people, let enterprise executives really control and coordinate manufacturing process anytime and anywhere, broaden the depth, breadth and transparency of information in manufacturing process for enterprise executives, help enterprises improve capital turnover speed and market sensitivity, greatly reduce costs, and improve enterprises. Response speed and efficiency, completely eliminate waste, in order to quickly enhance the core competitiveness.
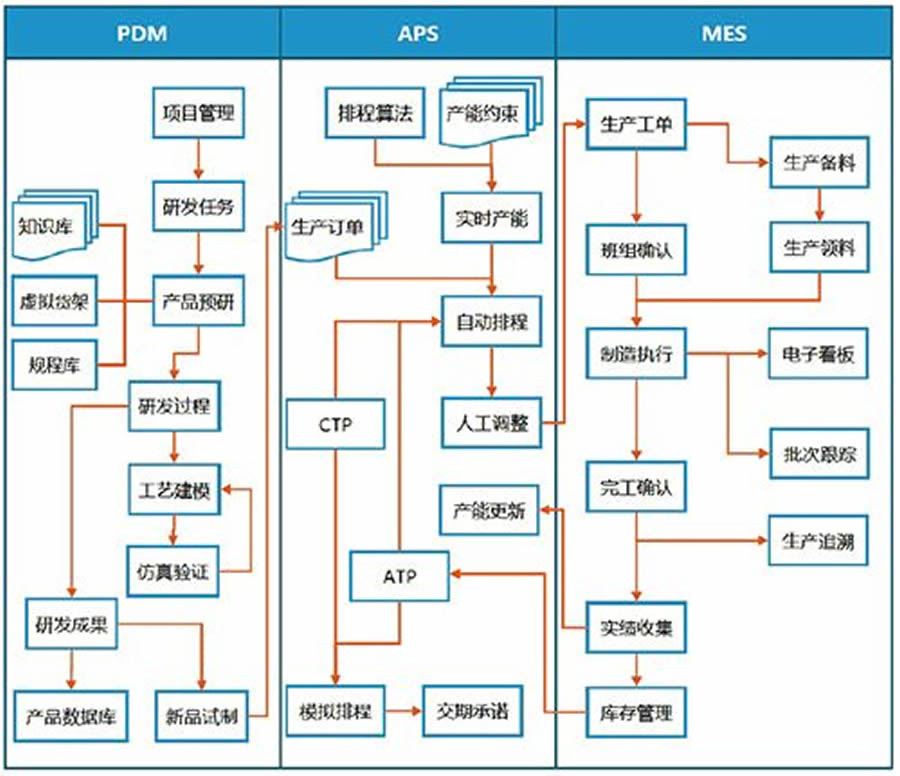
Feature 2: dynamic data
Lean production solution (APS + MES system) is integrated with production equipment and field hardware to give full play to its maximum efficiency, realize real-time data collection, dynamic analysis, dynamic statistical processing, and truly achieve the purpose of real-time control! No matter long-term or short-term plan, no matter weekly plan, daily plan, equipment plan, lean production solution (APS + MES system) can provide optimized plan mode, and continuously roll calculate the implementation of the plan.
Feature 3: Intelligent response, forming a new plan
The lean production solution (APS+MES system) is an intelligent system that responds according to the actual situation of the production site. It automatically adjusts the next step according to the information changes of materials, production capacity, fixtures, equipment abnormalities, attendance personnel, etc. Plan to form a new plan. Make optimal arrangements based on actual conditions to solve manufacturing synchronization problems!
How the programme works 1. The production plan of the new order is automatically arranged and calculated by the lean production solution (APS + MES system) according to the product processing route, materials, processes, equipment, personnel, delivery time, etc., and then released in an optimized way.;
2. Large screen LED production Kanban, full-color LCD Kanban let your production site progress more clear and transparent, at a glance. Through wired or wireless AP mode to achieve all-round network coverage, abnormal production is timely sent to the relevant personnel's mobile phones for processing, and the production progress is automatically entered into the host server system for analysis and statistical processing. With it, you can view the order production information anywhere in the world where there is network signal, to meet the customer's documentary demand.;
3. The sensor acquisition equipment automatically transmits information back to the lean production solution (APS + MES system), and the lean production solution (APS + MES system) automatically and rapidly analyzes the progress and manufacturing status of various products, forming tens of thousands of statistical tables, providing accurate basis for making effective decisions, building the most efficient and agile organization system, and large enterprises can also respond. Equally sensitive;
4. Say goodbye to the overwhelming paper, say goodbye to the mistakes caused by the manual list, and incorporate all the drawing forms and documents such as the task processing list, QC engineering drawing, processing drawing and report list into the PLC industrial touch screen terminal, so that the operator can transfer out the data required for the internal production of post responsibilities more quickly and conveniently, reduce the errors and search time, and avoid the phenomenon of data loss.;
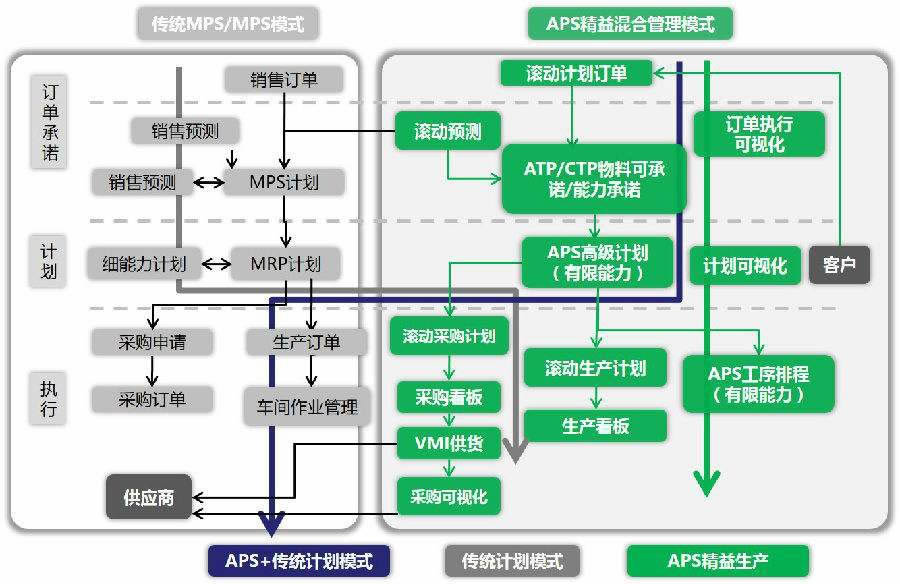
5. Due to the lag of information, it is usually yesterday's or earlier reports and exception handling applications that are placed on the desks of managers. Through the lean production solution (APS + MES system), there is no need for the documentary or statistician to repeat the tedious work, and no need for the level-1 and level-1 reporting and exception handling. These are all completed by using the world's top-level terminal hardware acquisition system, so that you can sit in the office within seconds and understand all the information of each order manufacturing through the host server.
Prospects for development ERP has basically solved the problem of purchase, sales and inventory, but for manufacturing enterprises, the real bottleneck of planning and scheduling cannot be solved by ERP. At this time, lean production solution (APS + MES system) has become an IT solution that must be considered in the post ERP era.